+86 180 5061 9999
247004145@QQ.COM
No. 35 Cifu Road, Economic Development Zone, Muyang County, Suqian City, Jiangsu Province
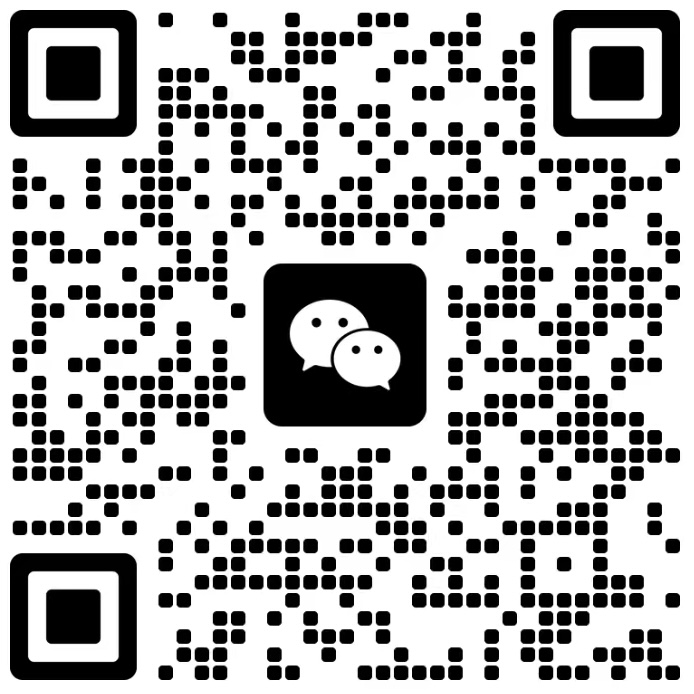
Types of Coatings - Acrylic Coating
Time : 2024-09-02
The main types of coatings currently used for canned food include epoxy phenolic coatings, epoxy amino coatings, organosol coatings, vinyl coatings, polyester coatings, acrylic coatings, and epoxy ester coatings. Below is a brief introduction to the characteristics of various resins, as well as their properties and applications after being made into coatings.
Acrylic Coating
At present, the acrylic resin used for metal surface coating is mainly solvent based thermosetting, which can be separately formulated into base enamel and surface varnish. Due to the relatively poor adhesion and flexibility of the acrylic resin used for painting compared to polyester. So, currently most acrylic resins are rarely formulated as base enamel, but are more commonly used as surface varnish for beverage and food cans and miscellaneous cans.
Ink has good compatibility. At present, the
(2) The external application of gloss oil requires good plumpness, so the viscosity of the coating and the thickness of the coating film should be controlled during construction. When the viscosity is too low, there may be insufficient material on the rubber roller, resulting in a thinner coating thickness and affecting the gloss and fullness of the product. However, it is also necessary to prevent problems such as leveling and adhesion caused by high viscosity.
reactive functional groups of acrylic resins are mainly provided by introducing monomers such as hydroxyethyl methacrylate, hydroxypropyl ester, epoxy propyl ester, butyl etherified N-hydroxymethacrylamide, and acrylic acid to provide active functional groups such as hydroxyl (- OH), carboxyl (- COOH), and amino (- NHCH2OBu), which react with various melamine resins, blocked isocyanates, or their own active functional groups, and crosslink into films under high temperature baking to obtain coatings with the desired properties. For three piece beverage and food cans, in addition to good adhesion, pencil hardness, and high gloss, their varnish also requires excellent wear resistance, scratch resistance, impact resistance, and water vapor sterilization to maintain high gloss.
To meet the above requirements, the main acrylic resin should first provide a suitable molecular weight Mn: 4000~8000. Resins with low molecular weight have poor adhesion and impact resistance. Resins with high molecular weight have high viscosity, resulting in low solid content and high viscosity when formulated into coatings, which is not conducive to coating application. Secondly, the glass transition temperature range of the resin should be controlled within the range of 10-70 ℃. The low glass transition temperature of the resin indicates that there are too many long-chain alkyl groups in the monomer, such as butyl acrylate, isooctyl acrylate, etc. The long alkyl chains of these monomers increase the rotational space of the polymer and act as plasticizers; At the same time, it will reduce the reaction rate of the resin, which is not conducive to the stain resistance and water vapor resistance of the coating, and may cause adhesion problems during the production of coating iron. However, excessively high glass transition temperatures can result in poor adhesion and impact resistance due to their high cohesive energy; It will also cause problems such as high viscosity of the coating, low solid content, which is not conducive to construction and affects the fullness of the varnish
For acrylic resins used in can coatings, most amino resins and end capped aliphatic isocyanates have good miscibility with them. Amino resin provides excellent reactivity, stain resistance, hardness, and chemical corrosion resistance. Aliphatic isocyanates can enhance the toughness and wear resistance of varnish, but the solvent resistance of this system is relatively poor. Due to the fact that thermosetting acrylic resins mainly rely on their hydroxyl or carboxyl groups and crosslinking agents for reaction, catalysts with different acidity should be selected for amino resins with different degrees of etherification for catalysis. For blocked isocyanates, different curing temperatures and active metal catalysts should be selected based on the blocking groups for curing reactions.
Key points for the construction of acrylic coatings: Acrylic coatings used for canned goods are mainly used as the main resin for external coating or edge seam external repair coatings. According to the purpose of the coating and the characteristics of the main resin, some special features are determined during its construction.
(1)The intrinsic tensile properties of acrylic resin are not very good, and the cross-linked functional groups are distributed on the side of the molecular chain. The interpenetrating network structure formed when the coating is heated and crosslinked further restricts the activity within and between molecules, resulting in a coating with certain hardness and toughness. If high imine or melamine resin with a certain degree of etherification is used in the coating, the curing temperature will be too high, causing the coating to become brittle and the adhesion to deteriorate. This can easily lead to coating scratches or peeling at the edges and necks during canning, canning, and transportation. For this type of coating, the curing temperature must be controlled.
Related Articles
感谢您与我们分享您的满意程度
请让我们知道更多
谢谢你!我们会认真查看你的留言