+86 180 5061 9999
247004145@QQ.COM
No. 35 Cifu Road, Economic Development Zone, Muyang County, Suqian City, Jiangsu Province
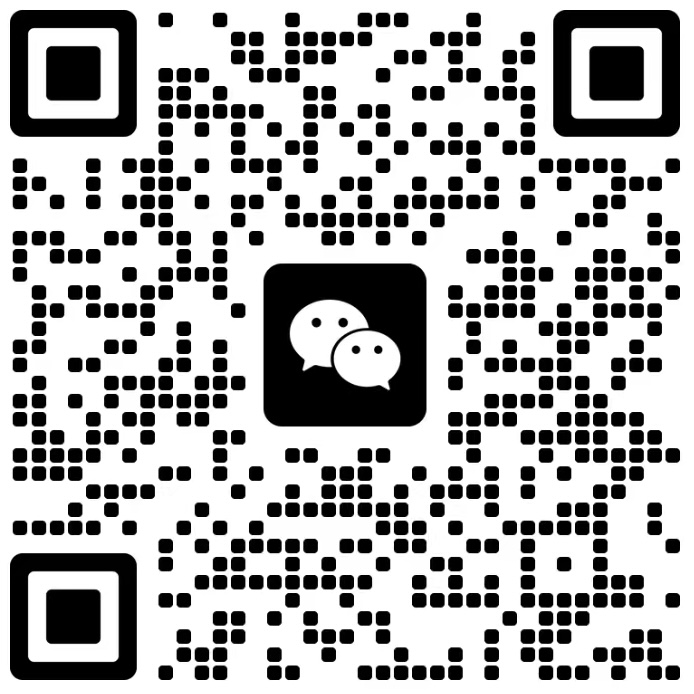
Enhance metal protection with polyester coating
Time : 2024-09-04
· Polyester coating
Polyester resin is a product of the combination of multifunctional alcohols and multifunctional acids. Polyester does not contain fatty acids (unlike alkyd resin), so it is sometimes referred to as "oil-free alkyd resin". It can provide better coating color stability or non yellowing, thus surpassing the alkyd resin series of coatings. Magnetic paint and topcoat that can be used for various purposes such as beverage and food cans, unscrewed lids, crown lids, and miscellaneous cans.
Due to the composition of polyester, resin manufacturers are able to design polyester resins with different hardness and flexibility properties. The adhesion of polyester can be said to be the best currently used in the field of metal coating printing. Its adhesion advantage to tinplate is quite obvious, and it can be used as a base varnish, topcoat, or colored enamel. In addition, the presence of more polar groups makes its wetting performance on TiOz very excellent, which can effectively increase the coating's covering power, gloss and other properties. The stretchability of molecular chains is higher than that of acrylic and epoxy esters, and coatings will exhibit better impact resistance and processability. As a varnish, the hardness of polyester coatings is slightly lower than that of acrylic or epoxy ester coatings, but the coatings exhibit better toughness and wear resistance after curing into a film. Choosing the appropriate crosslinking agent and increasing its dosage can compensate for the poor water vapor resistance of the main resin itself. It exhibits excellent water vapor resistance and maintains high gloss after sterilization in high-temperature sterilization tanks. The main properties and advantages of polyester coatings are as follows:
• High flexibility;
• Excellent adhesion to metal substrates, therefore no need for primer coating;
• Good color fastness of the coating film;
• High solid content.
The selection of the main resin is crucial for designing qualified polyester coatings. Firstly, the molecular weight of resin is a crucial parameter. At present, the molecular weight of polyester used for external coating should generally be controlled within the range of Mn: 3000-10000. If the molecular weight is too small, the adhesion of the coating will deteriorate, and the addition of polar groups will also affect the gloss of food cans after sterilization. If the molecular weight is too high, the coating will reflect many characteristics of thermoplastic coatings, such as poor cross-linking, lack of water vapor sterilization, and coating loss of gloss; The problem of sticking to the board may occur during coating, and the viscosity of the coating may be too high, resulting in low sensitivity to solid content, which is not conducive to coating application. Secondly, the glass transition temperature of polyester is also an important parameter. The glass transition temperature is too high, and the viscosity of the resin is too high, which is not conducive to the formulation of coatings. At the same time, the cohesive energy of the resin itself increases too quickly, which can also reduce the adhesion and impact resistance of the paint film.
The combination of polyester resin and various fermented amino resins can demonstrate a good combination of hardness and toughness, and improve water vapor resistance, stain resistance, and solvent resistance. Benzene based resin can give coatings a good initial gloss and certain chemical resistance. The combination of polyester and isocyanate can improve the flexibility and processability of the coating. At the same time, the low activation energy of isocyanate can reduce the film-forming temperature. The above crosslinking agents can be selected and matched according to the specific requirements of the coating to achieve polyester coatings that meet the requirements for metal can use.
Key points for the construction of polyester coatings: Due to the wide reaction conditions of polyester itself, the comprehensive performance of resin flexibility and hardness is relatively good, and the construction conditions are not very strict. The curing temperature of the coating can be adjusted according to specific application scenarios.
The recently developed coatings crosslinked with polyester resin and phenolic resin can also be used for coating food cans with light corrosiveness. If the coating is required to be a non PVC system or epoxy resin free, polyester formaldehyde coating is a better alternative. However, its chemical resistance is still slightly inferior compared to epoxy phenolic coatings, which limits its application in highly corrosive food.
The combination of polyester organosol can also be used as an inner wall coating for many acidic and sulfur-containing food packaging
Polyester, as the main component of powder coating, is also used for repairing the welds on the inner walls of three cans. After the three piece can body is formed by resistance welding, there is still exposed metal substrate at the welding point, and powder coating provides protection at the weld seam. The advantages of powder coating are as follows:
• 100% solid technology, with no volatile organic compounds (VOCs) compared to liquid coatings;
• Comply with environmental regulations;
• Due to the thick coating and good covering performance, a dense coating layer is formed (higher than liquid touch up paint).
Powder coating is usually white, but there can also be gray and transparent types.
Powder coating is applied in the form of electrostatic spraying, in which the powder forms a flow state through air flow and charges the powder particles (corona charging or friction charging). Due to the opposite nature of the charges, the charged particles will be transferred to the substrate and attached to the metal. After the coated relay head is put into the furnace, it generally needs to be baked at 232-260P for 8-10 seconds to melt the fine powder particles and form a uniform and continuous coating. The heating process does not involve any chemical process, only melting and flowing, and then forming a thermoplastic coating after cooling. Due to its excellent chemical resistance and mechanical processing properties, thermoplastic polymer can be used in almost all three piece food cans.
In order to achieve protection of the inner wall weld seam, the quality of powder coating must meet the following physical, chemical, mechanical processing performance and regulatory standards:
• Good fluidity and appearance;
• Achieve good protection with minimal coating thickness;
• Can carry an electric charge;
• Liquidity;
• Corrosion resistance/low porosity;
• Mechanical strength/flexibility;
• Steaming and boiling resistance;
• Chemical resistance (food packaging testing, solvent resistance);
• Low mobility;
• Compliant with FDA 175.300 and EU regulations.
Related Articles
感谢您与我们分享您的满意程度
请让我们知道更多
谢谢你!我们会认真查看你的留言