+86 180 5061 9999
247004145@QQ.COM
No. 35 Cifu Road, Economic Development Zone, Muyang County, Suqian City, Jiangsu Province
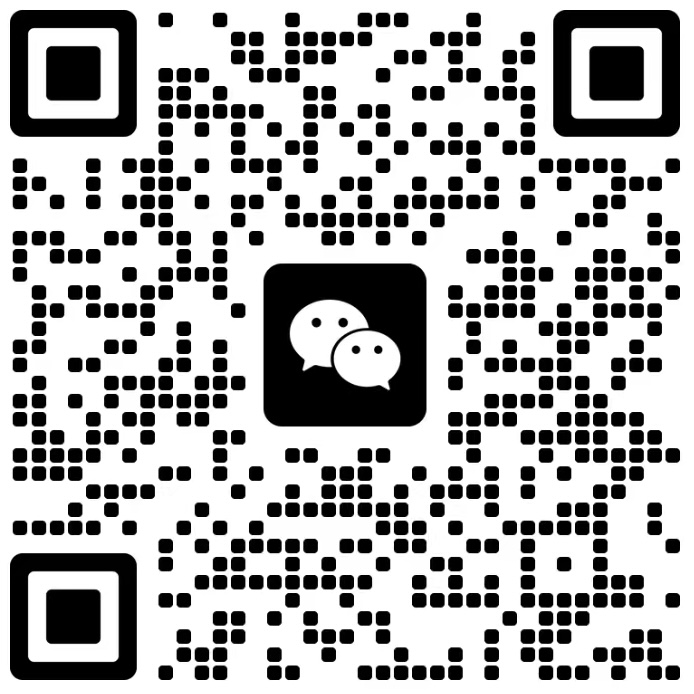
Characteristics and Application of Resin in Beverage Can Coatings
Time : 2024-09-04
The main types of coatings currently used for canned food include epoxy phenolic coatings, epoxy amino coatings, organosol coatings, vinyl coatings, polyester coatings, acrylic coatings, and epoxy ester coatings. Below is a brief introduction to the characteristics of various resins, as well as their properties and applications after being made into coatings.
·Epoxy phenolic coating
Epoxy phenolic coating is a coating system mainly composed of epoxy resin and phenolic resin, formulated in a certain proportion. It is widely used in the field of canned metal packaging, especially in the coating of inner walls of beverage and food cans.
Epoxy resin refers to a high molecular weight polymer containing 2 or more epoxy groups, with aliphatic, cycloaliphatic, or aromatic segments as the main chain. Epoxy group is a characteristic functional group of epoxy resin, and its content is the most important indicator of this resin. In three beverage and food cans, high molecular weight epoxy resins are usually required, such as type 7 and type 9 epoxy resins or even higher molecular weight epoxy resins, which have good impact strength and toughness. Due to the large number of oxygen-containing functional groups on the molecular chain, they have good adhesion; Phenolic resin is a resin obtained by condensation reaction of phenolic monomers and aldehyde monomers. It is composed of a large number of methylene groups (CHz -) and rigid phenolic bonds. The structure contains a large number of polar phenolic hydroxyl groups, and the molecular structure has high rigidity but poor flexibility. The hydroxyl groups on the molecule further solidify to form a three-dimensional structure composed of C-C bonds in a network. Due to its tight structure, it is relatively stable to various chemicals, so phenolic resin has good corrosion resistance, especially outstanding acid resistance. Therefore, epoxy phenolic coatings have the different advantages of two types of resins:
·Good adhesion to metal substrates;
·Excellent processability;
·Excellent chemical resistance (sulfur and acid resistance in food packaging);
·Good heat resistance and wear resistance;
·Low shrinkage rate and low porosity.
Due to its excellent corrosion resistance, epoxy phenolic coatings play a very important role in three piece beverage and food cans, as well as in two piece deep drawn food cans. For example, they are used as inner coatings in various fruit juices, herbal teas, and high acid, high sulfur food cans. Usually, epoxy phenolic coatings display a golden yellow color, with a bright and full color, as well as excellent physical properties (wear resistance and flexibility) and resistance to cooking. Therefore, epoxy phenolic coatings are often used for coating inside miscellaneous cans and for coating the top and bottom covers of beverage and food cans.
A single application of epoxy phenolic coating requires baking at 200-205 ° C for 10 minutes to fully cure. Of course, many epoxy phenolic coatings can also achieve complete curing after multiple baking at lower temperatures. However, after multiple baking cycles, the adhesion of epoxy phenolic coatings can easily decrease sharply, seriously affecting the quality of the coating. Moreover, the darker the coating color, the more attention should be paid to the curing temperature and coating process during the coating process. While ensuring complete curing of the coating, the number of baking cycles should be minimized as much as possible.
Epoxy phenolic coatings have good wetting and leveling properties on substrates such as tinplate, plated iron, and aluminum plate, and are not prone to common surface defects. Of course, this is also closely related to the surface treatment of the substrate. During the coating process, attention should be paid to the construction viscosity. If the viscosity is too high, it will affect the leveling effect of the coating and even cause surface defects. If the viscosity is too low, it is easy to cause sagging. In practical operation, special diluents should be used according to the coating for dilution. In addition, due to the presence of appropriate additives in the coating system, the coating needs to be thoroughly stirred before use to ensure its uniformity. Aluminum paste or zinc oxide is often added to epoxy phenolic coatings for packaging high sulfur foods such as meat, seafood, asparagus, etc. The release coating made by adding release wax to the above system can also be used for packaging canned luncheon meat. The main function of aluminum paste is to block the hydrogen sulfide generated during food sterilization from passing through the coating and covering the possible sulfide spots. The main function of zinc oxide is to absorb the hydrogen sulfide generated during food sterilization and prevent sulfide corrosion. However, the addition of aluminum paste or zinc oxide to epoxy phenolic coatings can result in a softer coating and a decrease in processability.
Related Articles
感谢您与我们分享您的满意程度
请让我们知道更多
谢谢你!我们会认真查看你的留言